Introduction
In today's fast-paced world, the ability to monitor and diagnose equipment remotely is becoming increasingly important. This is especially true for critical systems like diesel generators, which are often used in remote locations where immediate access to technicians may not be feasible. Remote diagnostics technology has emerged as a game-changer in this regard, allowing operators to monitor the health and performance of their diesel generators from anywhere in the world. In this article, we will explore the impact of remote diagnostics on diesel generators and how this technology is revolutionizing the way these essential power sources are managed and maintained.
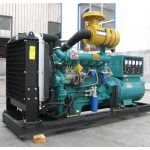
Understanding Diesel Generators
Diesel generators play a crucial role in providing backup power in a wide range of applications, from hospitals and data centers to remote construction sites and off-grid locations. These generators are known for their reliability, durability, and ability to provide continuous power for extended periods. However, like any complex machinery, diesel generators require regular maintenance and monitoring to ensure optimal performance and prevent unexpected downtime.
Traditionally, monitoring the health and performance of diesel generators involved manual inspections, routine maintenance schedules, and reactive troubleshooting when issues arose. This approach was not only time-consuming and labor-intensive but also prone to human error and oversight. In remote locations, where access to skilled technicians may be limited, diagnosing and resolving generator issues in a timely manner presented significant challenges.
The Emergence of Remote Diagnostics Technology
Remote diagnostics technology has transformed the way diesel generators are monitored and maintained. By leveraging the power of the Internet of Things (IoT) and advanced sensor technology, remote diagnostics systems allow operators to track key performance metrics, detect potential issues, and diagnose problems in real-time, all from a centralized dashboard accessible via a computer or mobile device.
These systems are equipped with a wide range of sensors that continuously monitor critical parameters such as engine temperature, oil pressure, fuel levels, and battery voltage. Any deviations from normal operating conditions trigger alerts that are sent to operators, enabling them to take proactive action before a minor issue escalates into a major problem. In addition to real-time monitoring, remote diagnostics systems also store historical data and generate predictive maintenance schedules based on usage patterns and performance trends.
Benefits of Remote Diagnostics for Diesel Generators
The adoption of remote diagnostics technology has brought about a multitude of benefits for operators of diesel generators, including:
1. Improved Reliability: By monitoring key performance indicators in real-time, operators can identify potential issues before they cause a breakdown, reducing the risk of unexpected downtime and ensuring continuous power supply.
2. Enhanced Safety: Remote diagnostics systems allow operators to detect hazardous conditions such as overheating or fuel leaks remotely, minimizing the need for on-site inspections and reducing the risk of accidents.
3. Cost Savings: Proactive maintenance enabled by remote diagnostics helps to extend the lifespan of diesel generators, reduce repair costs, and optimize fuel efficiency, leading to significant long-term cost savings.
4. Remote Troubleshooting: In the event of a problem, technicians can remotely access the diagnostic data and troubleshoot the issue without the need for a physical visit, saving time and resources.
5. Data-Driven Decision-Making: The wealth of data collected by remote diagnostics systems enables operators to make informed decisions about maintenance scheduling, spare parts inventory, and equipment upgrades, maximizing operational efficiency.
Case Studies: Real-World Applications of Remote Diagnostics in Diesel Generators
Let's take a look at some real-world examples of how remote diagnostics technology is being used to monitor and manage diesel generators in diverse applications:
1. Telecommunications Industry: In the telecommunications sector, diesel generators are often used as backup power sources for cell towers and communication infrastructure. Remote diagnostics systems allow network operators to monitor the health of their generators across multiple sites, identify performance issues, and dispatch technicians only when necessary, minimizing downtime and ensuring uninterrupted service for customers.
2. Mining Operations: In remote mining sites where access to skilled technicians is limited, remote diagnostics technology is invaluable for monitoring the fleet of diesel generators that power heavy machinery and equipment. By proactively addressing maintenance issues and optimizing fuel consumption, mining companies can improve operational efficiency and reduce downtime, ultimately increasing productivity and profitability.
3. Healthcare Facilities: Hospitals and medical facilities rely on diesel generators to maintain critical services during power outages. Remote diagnostics systems enable facility managers to remotely monitor the performance of their generators, receive alerts in case of any anomalies, and take swift action to ensure uninterrupted power supply for life-saving equipment and patient care.
4. Off-Grid Communities: In off-grid communities that rely on diesel generators for electricity, remote diagnostics technology offers a cost-effective solution for monitoring and managing power generation systems. By remotely tracking fuel consumption, engine performance, and maintenance requirements, community leaders can optimize the operation of their generators and ensure reliable power supply for residents.
Challenges and Considerations
While remote diagnostics technology holds great promise for the management of diesel generators, there are several challenges and considerations that operators and technicians need to keep in mind:
1. Data Security: As remote diagnostics systems collect a vast amount of sensitive data about generator performance and maintenance activities, ensuring data security and protecting against cyber threats is paramount.
2. Connectivity Issues: In remote or rural locations with limited internet connectivity, accessing real-time diagnostic data and troubleshooting remotely may be challenging. Operators should consider alternative communication methods or offline data storage options to address this issue.
3. Technician Training: Remote diagnostics systems require operators and technicians to have the necessary training and expertise to interpret diagnostic data, perform remote troubleshooting, and make informed decisions about maintenance and repairs.
4. Integration with Existing Systems: Integrating remote diagnostics technology with existing generator control systems and maintenance workflows may require careful planning and coordination to ensure seamless operation and optimal performance.
Future Trends and Innovations
Looking ahead, the field of remote diagnostics for diesel generators is poised for further advancements and innovations. 30kw diesel generator of the key trends to watch out for include:
1. Artificial Intelligence and Machine Learning: By leveraging AI algorithms and machine learning models, remote diagnostics systems can analyze vast amounts of data to predict equipment failures, optimize maintenance schedules, and recommend performance improvements, ultimately enhancing the reliability and efficiency of diesel generators.
2. Edge Computing: Edge computing technology enables data processing and analysis to be performed at the source, closer to the generator, reducing latency and enhancing real-time monitoring capabilities, especially in remote or bandwidth-constrained environments.
3. Blockchain Technology: Blockchain offers a secure and transparent way to store diagnostic data, maintenance records, and equipment history, providing a tamper-proof audit trail for operators and technicians to track the lifecycle of diesel generators and ensure compliance with regulatory requirements.
4. Predictive Maintenance as a Service (PMaaS): By partnering with third-party service providers that offer predictive maintenance solutions as a service, operators can leverage expert knowledge, advanced analytics tools, and industry best practices to optimize the performance of their diesel generators and maximize uptime.
Conclusion
Remote diagnostics technology is revolutionizing the way diesel generators are monitored, maintained, and managed, empowering operators to proactively address maintenance issues, optimize performance, and ensure continuous power supply in diverse applications. By embracing this transformative technology and staying abreast of the latest trends and innovations, operators can unlock new opportunities for efficiency, reliability, and cost savings in their diesel generator operations. As we continue to push the boundaries of remote diagnostics capabilities, the future looks bright for the seamless integration of technology and machinery in the quest for operational excellence.